WILLMAR, Minn. — Grabbing onto business opportunities that blend innovative engineering skills and rapidly advancing 3-D printing technology, three brothers are expanding their role in digital manufacturing that could be a game-changer for all manufacturers — and a benefit to consumers.
Brothers Carl, Brian and Sean Douglass have grown DI Labs at their new location in Willmar, Minn.
ADVERTISEMENT
was started in 2013 in Spicer, Minn. As their technology advanced and their 3-D printing equipment evolved — and their client base expanded — the business outgrew the space in Spicer. The new, larger location in Willmar has been in full operation for a month.
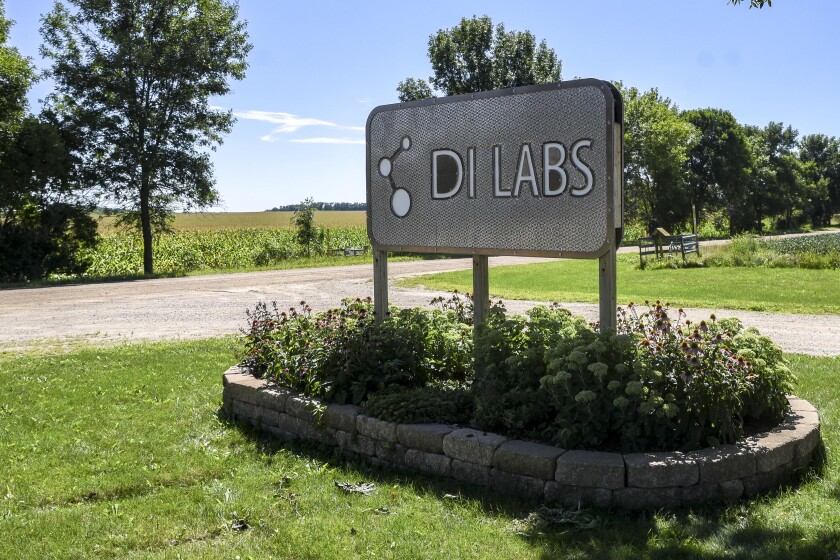
In the midst of the move, the company's cutting-edge technology was used to respond to a shortage of medical equipment caused by COVID-19 and, at the request of a customer, DI Labs began printing face shields that fit over a hard hat.
During a media tour Tuesday, Aug. 18, that included a live, virtual broadcast, DI Labs President Carl Douglass referred to the heart of the 20,000-square-foot building, officially called the “innovation center,” as the “magic factory,” where designs developed by the engineering team are produced by about 25 different 3-D printers that hum (some not so quietly) in spotless rooms.
The business is a combination of engineering and manufacturing with the goal of finding solutions to problems and serving as an “education resource for additive manufacturing,” Douglass said.
Unlike subtractive, or traditional, manufacturing that, for example, takes a block of metal and shaves and molds it into a product, additive manufacturing “makes something from nothing,” he said.
ADVERTISEMENT
The “nothing” used by DI Labs includes products like plastic powder, liquid polymer or metal filaments that are printed in multiple layers to create something.
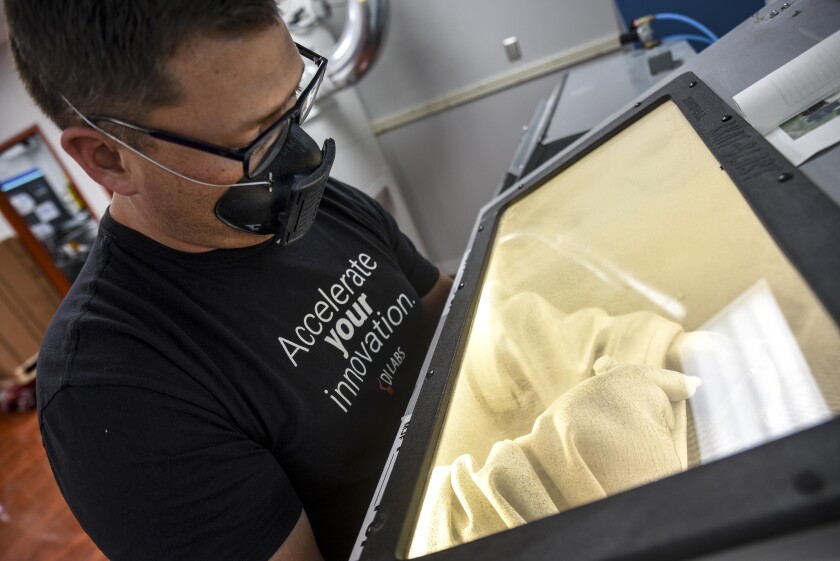
By “skinning our knees” and being the “first in the world” to develop certain technologies, Douglass said the company’s goal is to create a process that helps businesses get their products on the market faster and “serve people better.”
He said the development of the face shield is an example of how additive manufacturing can quickly respond to needs. He predicts there will be a “paradigm shift, both in the thinking and in the application of additive technologies for future cases.”
While DI Labs currently focuses on production of hard goods, Douglass said additive manufacturing technology has a place in many new venues in the future, including producing organs and tissue for medical applications.
The technology is currently unable to support mass customization of products, but Douglass said eventually businesses will be able to use additive manufacturing to make custom shoes for just one individual. “We’re not quite there yet with mass production, but we’re getting closer,” he said.
ADVERTISEMENT
Douglass said traditional manufacturing won’t go away and won’t be replaced with additive manufacturing, but instead the two will complement each other and “each manufacturing method is going to have its sweet spot.”
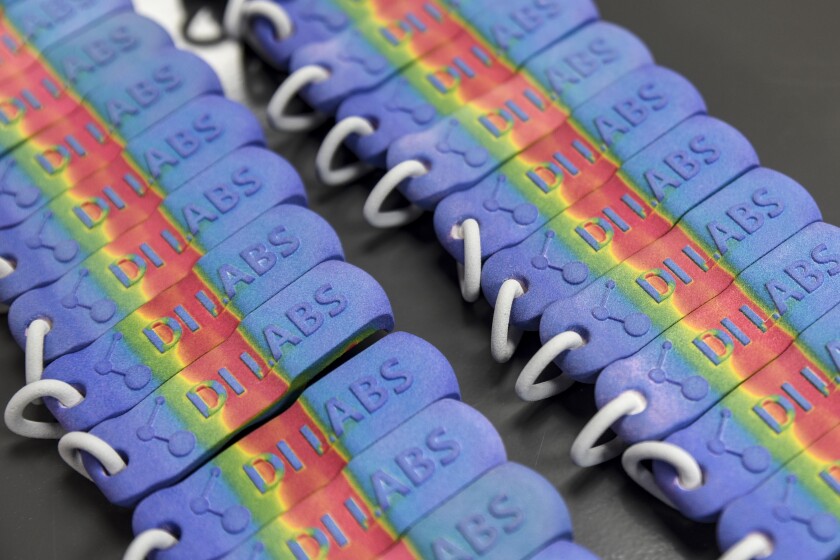
Douglass said rural Minnesota businesses doing traditional manufacturing should consider investing in their own additive manufacturing technology or working with a company like DI Labs.
He said that “additive manufacturing is changing the game for manufacturers and you’re either going to be able to leverage it for competitive advantage or your competitors are going to, but somebody is.”
The new DI Labs facility, in a former seed research facility, is surrounded by farm fields that will allow for a building expansion as the company's technology, production and list of clients grow.
Douglass said there are currently job openings at the lab, with plans to double their employee base by the end of the year.
ADVERTISEMENT
More info
For more information, go to the DI Labs .
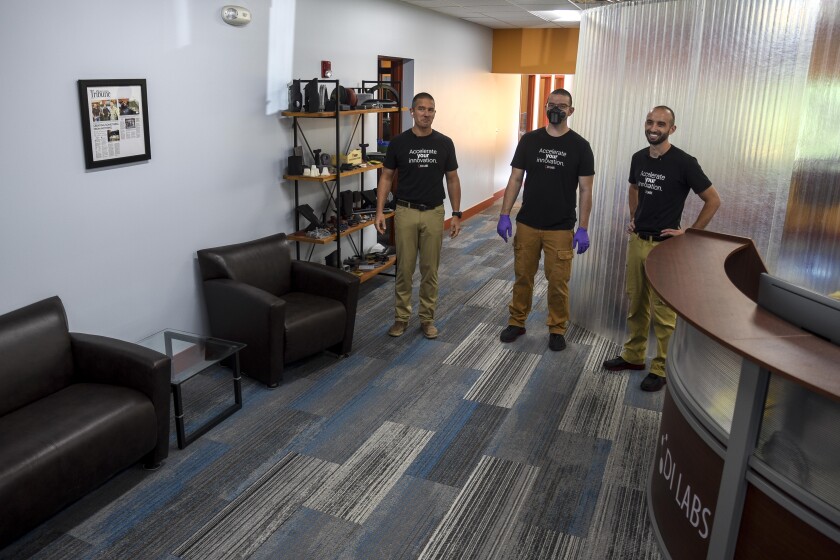
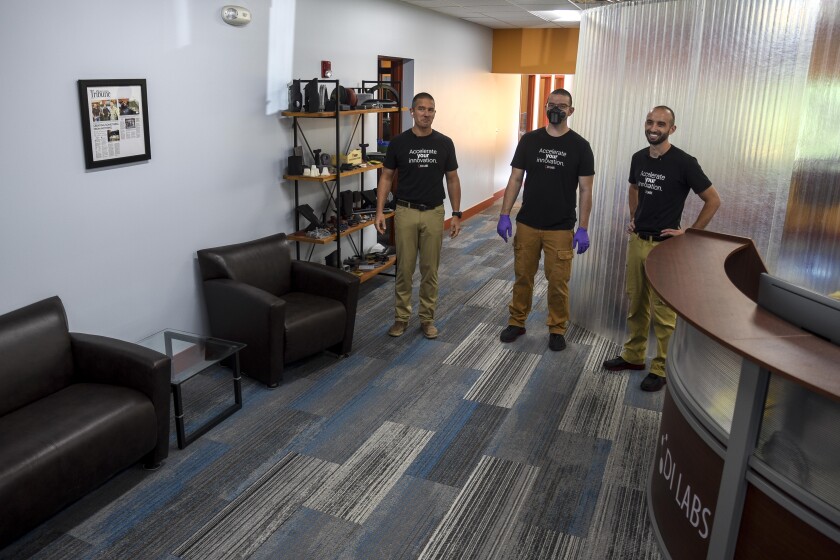